

This adjustment allows the hammerhead to be set at the proper height at the bottom of the stroke for the particular dies I am working with. I used ½ LH and RH heim joints so the length can be adjusted by just turning the tube and retightening the jamb nuts. The connecting rod is a piece of ¾ tubing with RH and LH nuts welded to the ends. This still gave more stroke than I wanted so now I have a 1/4 offset and the spring mount is moved back under the stroke limiter rubber. I wanted something closer to 4 of basic stroke so I drilled a 3/8 offset. I found that I had to move the spring mount way forward to get the head stroke under 6. The original offset was ½ for a total of 1 stroke. The eccentric is a piece of 2 round stock 1 thick welded to a ¾ axle and mounted in the ¾ pillow block bearings. I put a shorter leaf top and bottom to stiffen it up and also try to prevent the spring breakage some are experiencing with single leaf setups. The springs are from the old rear suspension of my MG project, they are 1 ¾ wide and ¼ thick. I used a flat head bolt in the rear position and extended the length of the top plate to give a longer flat surface the stroke limiter can bump against through its range of adjustment. I liked Jim Bailies latest spring mount because of the ease of stroke adjustability and spring length so I copied it. I painted the end of the arm Safety Orange to make it more noticeable and, hopefully, not get my head in the way when it is running. The arm is 36 long to the hammerhead and the back arm is 12 to the pushrod attachment. 060 wall tube spaced ½ apart that has been reinforced around the pivot attachment with 1/8 plate giving me something substantial to weld to.
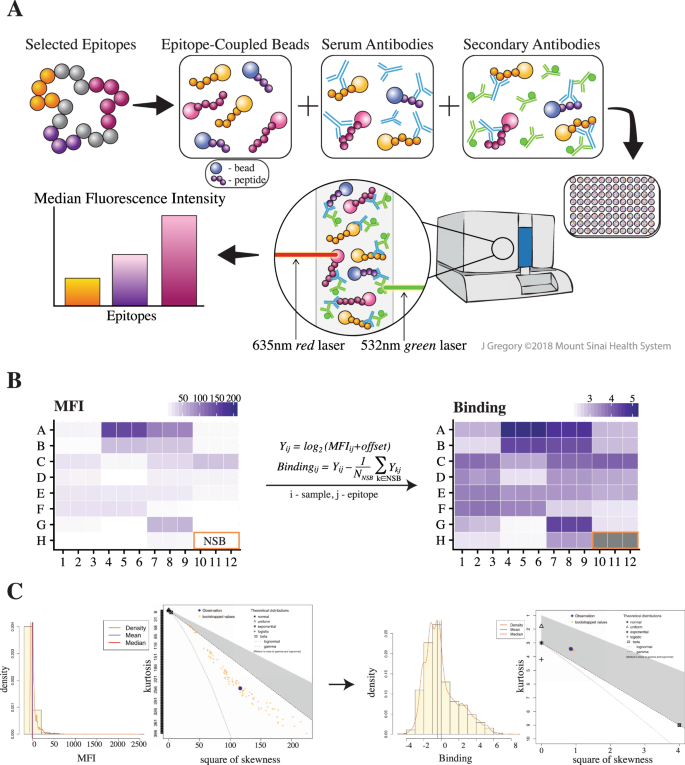
The top arm is made from 2 pieces of 1x2. I used 1 to mount the top arm and ¾ to hold the eccentric shaft. The pillow block bearings are a great deal from Northern Tool at $6.95 each for either ¾ or 1 sizes. It could have definitely been made from lighter material but I came across a bunch of 2 pieces of this stuff really cheap. The basic frame is 1 ½ square tube with 3/16 wall. I used a commercial sewing machine motor purchased on the Internet and made a foot pedal to operate the motors clutch through a linkage built into the table base. I also want to be able to use the motor and foot control for other, yet to be constructed, machines so it will be a permanent fixture below the benchtop and the future machines will also be benchtop mounted. I have made/bought too many big pieces of equipment and my once somewhat spacious shop is getting pretty crowded so I wanted to make a helve that I could mount to my bench when I needed it and could be stored away when I didnt. I am just finishing up rebuilding the frame on my English Wheel and will post pictures when it is done. It's a little slow raising it up because you have to walk back and forth so much if you are alone but is sure a lot easier and safer than trying to raise the car up to attach to the rotator. I drilled holes in the vertical so a bolt can be inserted through as a safety catch. The winch is mounted to the yoke so it pulls itself up the vertical member. I used two HF worm drive winches and ran the cable up and over two gate support V pulleys and back down to the sliding yoke. You had to somehow raise it up to get it into the rotator. The problem with most rotisserie designs I looked at was that you couldn't pick a car up off the floor. I made the ring roller to do a gentle curve in 1" round tube for a cowl edge but have used it for tons of other stuff since then. Moves metal in a hurry and hits about 300 beats per minute. Makes it handy to remove and store under a workbench when not in use. I built the helve to mount to my steel bench and run off a sewing machine motor mounted under the table. I have lifted a 750 lb bench mill out near the end a to load into a truck. The winch is a HF 1,300 lb and the mounting holes line up perfectly with the holes in the trolleys. The tracks are welded to a 2 x 4 x 1/8" tube 12' long.

The tracks and trolleys are for sliding barn doors and rated for 450 lbs each for a total of 900 lbs. Probably the handiest tool in the shop is the crane I built.
